JANUARY 25, 2023
Transitioning to Rental Packaging For Sustainable Clinical Operations
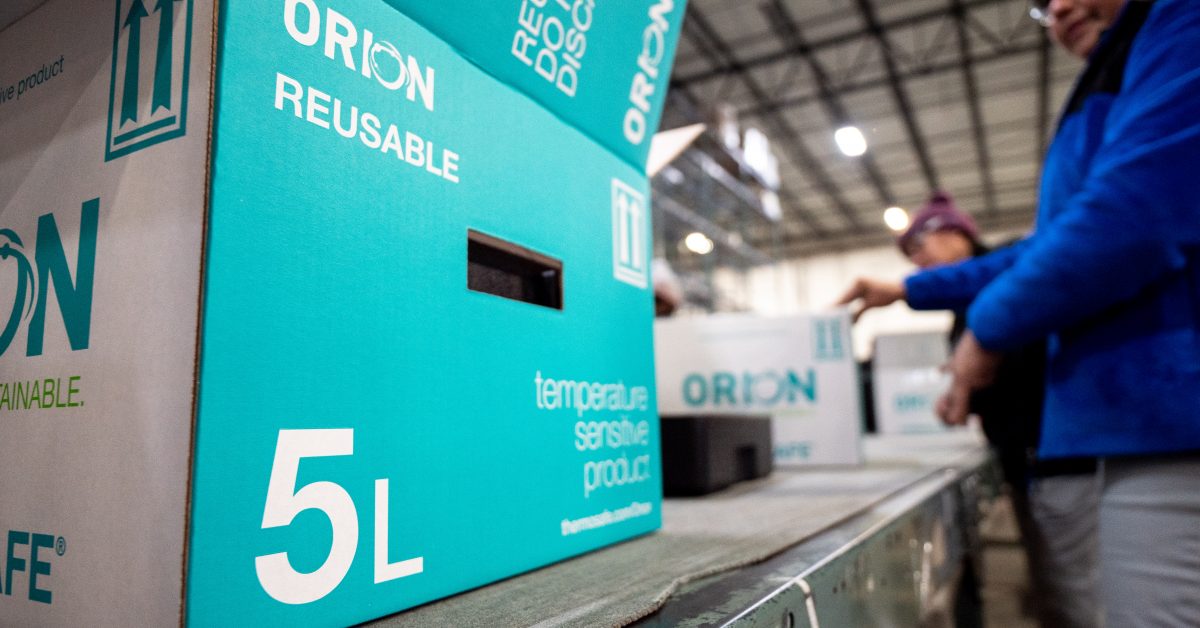
Change does not occur easily within in the pharmaceutical industry. There’s usually a pretty good reason. It typically boils down to cost, compliance, efficiency and the new kid on the block – sustainability. For one global biopharmaceutical company headquartered in California, it was a combination of several factors that created the business case to move from single-use packaging to rental parcel packaging for their US clinical operations.
Situation
A global biotechnology company based in California focused on antibody therapies was using disposable VIP shippers in their clinical supply chain. The VIP packaging was quite expensive and had relatively short validation time. The goal was to choose a shipper that could be globally qualified, giving the global clinical supply chain network the flexibility to implement the packaging at their site as well.
Solution
The Orion reusable packaging was chosen, the shipping system used within a completely redesigned rental parcel program for the biopharmaceutical industry.
- Removed 25,000+ boxes from the landfill
- Decreased the waste weight by 98%
- Over 50% cost savings per cold chain box including prepaid return logistics
- Increased qualified performance from 56 to 120 hours
Operations
Single-use boxes required greater operational management, including holding inventory in expensive GDP warehouse space and onsite conditioning equipment to prepare refrigerants for use. With older packaging systems, the components and pack out configuration were complex and cumbersome, also prone to human error.
The biotechnology company’s pack out time decreased by half from previous system to using the Orion
shippers that were delivered pre-conditioned ready to use.
Operational outcomes:
• Decreased cGMP warehouse and conditioning space commitment (pallets and floor space)
• Lighter tare weight decreased transportation & logistics costs for parcel sized packaging
• Significant decrease in assembly and packaging time
• Saved substantial labor costs

Performance
The goal of biotechnology company’s clinical supply was to prove that the new shippers would provide
superior price-to-performance ratio. This is a basic calculation of the per use cost divided by the
performance hours. For this solution, the ratio dropped significantly across all of the replacement sizes.
In moving to the Orion program, they went from 56 hours of validated performance to 120 hours. All four
sizes; 5L, 10L, 20L and 40L can be used for domestic or international shipping. This eliminated the need
to hold specialized inventory for long duration shippers. One packaging system met the requirements for
domestic and international shipping.
The biotechnology company realized:
• Over 50% cost savings per cold chain box including prepaid return logistics
• Increased qualified performance from 56 to 120 hours
• Reduced time-based excursions to domestic receiving sites
• Ability to ship on Fridays for Monday deliveries
Sustainability
Today most Biopharmaceutical companies have set fairly aggressive CSR or sustainability goals that
impact across the business and operations. The environmental impact goals usually include reduction of
greenhouse gas emission, renewable energy, reduction in landfill and waste.
The Orion reusable packaging program supports these sustainability goals thanks to the box’s robust design and ability to be disassembled and reconditioned for reuse. The fast expanding network of reclamation
stations also provides shorter distances back from customer sites. At End of Life (EoL), an Orion box is
largely recycled, minimizing impact to waste stream.
The Orion rental program, resulted in several rewarding outcomes for the biotechnology company:
• Significant reduction in the annual contribution to landfill sites
• Removed approximately 25,000+ boxes from the landfill
• Decrease the waste weight by 98%

Lessons learned
Performance Qualification
Regulatory agencies are asking more frequently for Performance Qualification (PQ) data in submissions,
particularily for cold chain products. This behooves the pharmaceutical company to conduct thorough
studies with well-documented reports.
The biotechnology company conducted internal PQ tests that showed the refrigerated boxes performed
well in advance of the current business standard of 96 hours. The Orions are qualified to 120 hours which
provides additional contingency during a shipment if there is an unexpected delays such as customs,
flight schedules, or weather disruptions.
In one instance, a shipping error with the carrier led to an Orion box being sent to the wrong receiving site.
Once the error was identified, there was enough qualified time in the Orion boxes where the product could
be retrieved and recovered.
Because the qualification was a collaborative effort between sites and departments, the PQ has been
designed in a way that other global sites can bring using the Orion boxes when they are ready.
Internal Stakeholder Alignment
Implementing a new system or technology requires a significant amount of time and stakeholder
engagement. Often times there are competing priorities between business process improvement,
compliance, and global standardization.
Fortunately, key stakeholders at the biotechnology company were already in the process of seeking out an
improved shipping soluton that would reduce complexity/inefficiencies, reduce cost, and be sustainable.
The initiation of this project on a local level helped create collaboration between corporate and regional sites.
For companies that are stalled in moving forward with rental, ask the tough questions:
• Is there a clear value proposition for reusable or rental packaging within your organization?
• Is there at least one champion that will take the lead?
• Is your organization comfortable outsourcing packaging operations?
Next
International Shipments
International shipments started October 2021 and expansion continues. Return networks for the Orions are
being rolled out in a phased approach based on region.